Fluid Bed Dryer Operation and Working Principle
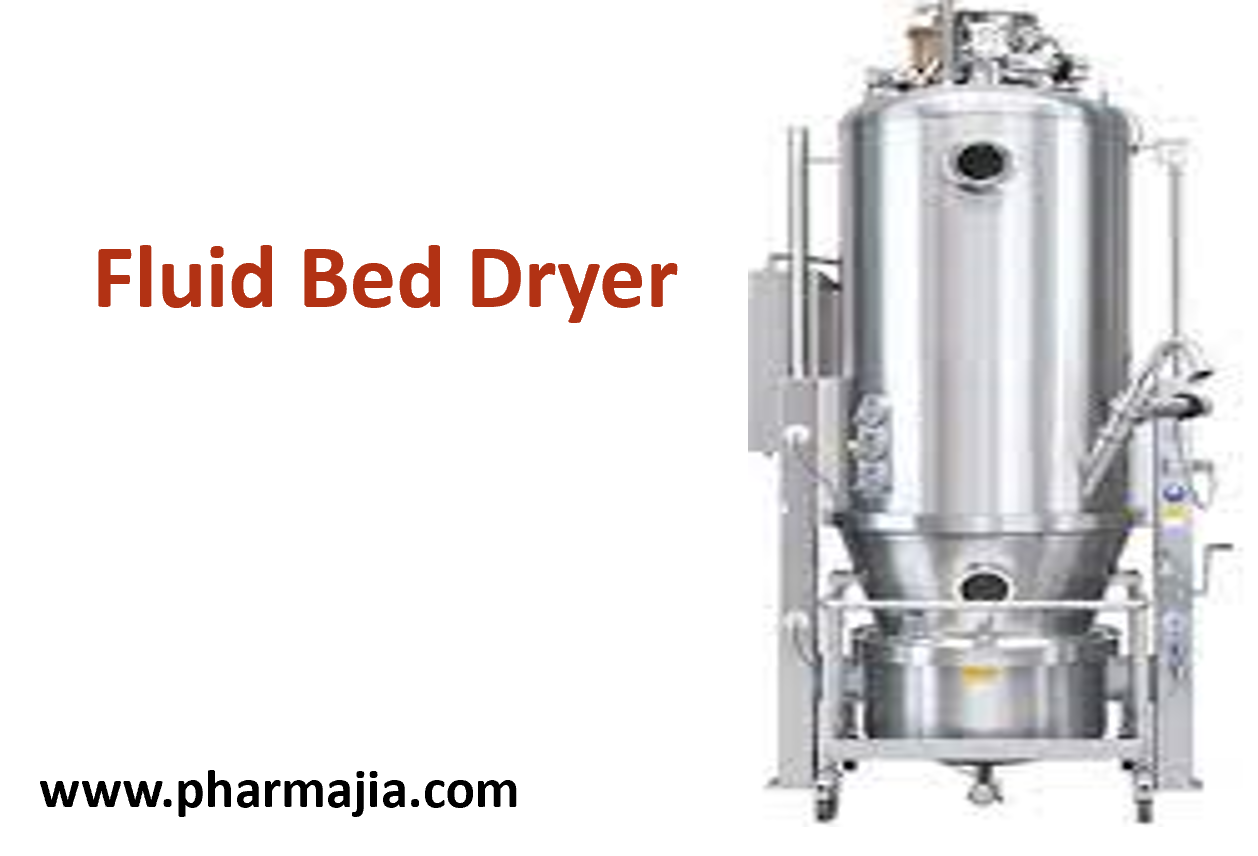
This article contains detailed information on Fluid bed dryer used in the pharmaceutical manufacturing operation.
What is mean by Fluid Bed Dryer ? and Its working principle ?
Fluid bed dryers are widely used in the pharmaceutical manufacturing for drying and processing of granular, crystalline, and powdery materials. They are highly efficient, energy-saving, and versatile.
It works on the principle of fluidization, drying, and cooling. The process starts by introducing a hot air stream through a perforated plate or distributor at the bottom of the drying chamber. The hot air stream passes through the product bed, causing the particles to become suspended in the air. This phenomenon is known as fluidization, which creates a fluid-like behavior in the bed of the product and results drying stage will happen.
What is mean by Fluidization ?
During fluidization, the particles in the product bed are separated and lifted, and the gaps between them are filled with air. The fluidization process enhances the heat and mass transfer between the particles and the airstream, resulting in efficient drying.
What are the components available in Fluid Bed Dryer ?
Several components available in Dryer, Some Major components are enlisted below,
- Inlet Air Filter
- Product container and Expansion Chamber
- Air Distribution Plate
- Exhaust air Filter
- Control Panel/HMI
Inlet Air Filter
The inlet air filter is the first component of a dryer that the incoming air passes through. It filters out any dust or contaminants from the air before it enters in Fluid bed dryer. This helps to ensure that the material being processed remains free from contaminants.
Product Container and Expansion Chamber :
The product container and expansion chamber is the major and cortical components of the fluid bed dryer. Powder material is storing in product container and is fluidized by a hot air stream.
Air Distribution Plate :
The air distribution plate is located at the bottom of the product container and distributes the hot air stream evenly through the fluid bed. The air distribution plate has holes or slots that allow the hot air to flow through it and into the fluid bed of product container. It is important that the air distribution plate is designed correctly to ensure that the hot air stream is evenly distributed through the fluid bed.
Exhaust Air Filter :
The exhaust air filter is the final component of the fluid bed dryer that the air passes through before being released into the atmosphere. It filters out any dust or contaminants from the exhaust air to prevent environmental pollution.
Control Panel/HMI :
The control Panel/HMI is responsible for controlling the various components of the dryer, such as the temperature, humidity, and air flow rate. It ensures that the fluid bed dryer operates at the desired conditions to achieve the desired drying result.
What is the application of Fluid Bed Dryer?
Fluid Bed dryer is used in the pharmaceutical manufacturing to drying and processing of different size material i.e. Granular, Crystalline, and Powdery.
Advantages of Fluid Bed Dryer
It is having the several advantages, Some of the enlisted as,
- Energy-Efficient
- Provide Uniform Drying
- For drying of all types of wet mass like Granular, Crystalline and powdery.
- Easy to Clean and Maintain
Disadvantages of Fluid Bed Dryer
It is also have some disadvantages, Some of the enlisted as,
- High Capital Investment
- Limited Capacity
What is difference Between Fluid bed Dryer and Fluid Bed Processor /Equipment?
A fluid bed dryer is a type of fluid bed equipment that is specifically designed for drying materials and A whereas fluid bed processor is a type of fluid bed equipment that can be used for various processes, such as Granulation, drying, coating, and agglomeration.