Operation of Pharmacode Reader
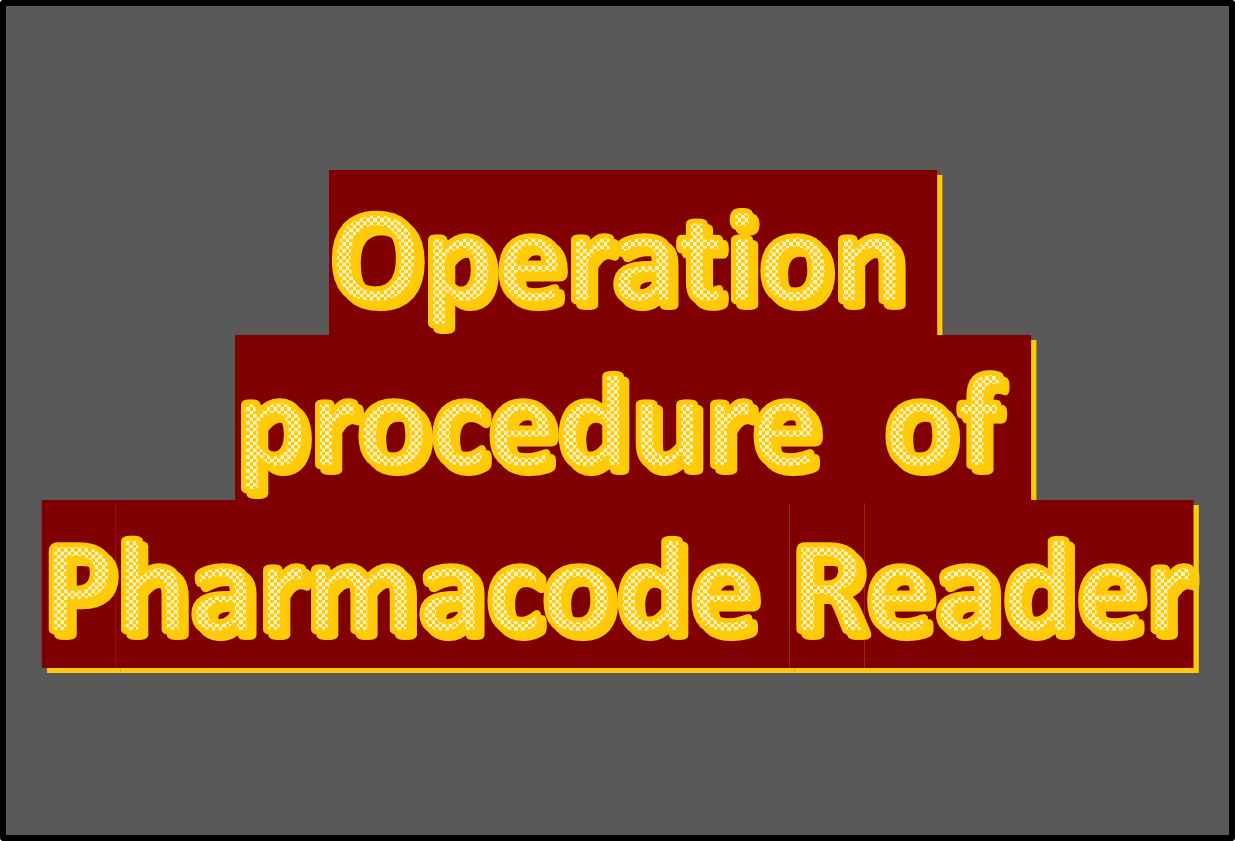
It describes the (Standard Operating procedure) SOP on Operation of Pharmacode Reader in Pharmaceutical Industry.
SOP on Operation of Pharmacode Reader
I. Purpose & Scope:
- To elaborate procedure for setting and operation of pharmacode reader/2D code reader and action in case of system failure while using pharmacode reader.
- Applicable to all pharmacode reader/2D code reader on cartonator, blister pack machine, tube filling and labelling machine, conveyer belt and during offline packing (If applicable)
II. Responsibilities:
- All Production, Engineering and quality Assurance personnel shall be responsible to follow and implement this SOP.
Definition of Pharmacode :
Pharmacode is a security control which is present on the different packaging material to differentiate and identify correct packaging material so as to avoid product mix up.
Refer Image :

Pharmacode
Definition of 2D code :
A Data Matrix code is a two-dimensional matrix barcode consisting of black and white “cells” or modules arranged in either a square or rectangular pattern. The information to be encoded can be text or numeric data.
Refer Image :

2 D Code
Procedure For Pharmacode Reader :
-
Setting of Pharmacode Reader for the Product:
- The procedure specified below is applicable for Argus or similar model.
- Switch on the Argus 6012. Insert the key in the key slot and turn the key in clockwise direction to Set Mode. Press F1 to go in main menu.
- Go to reference code using cursor key then press F2 key to program Pharmacode for packing material. For example, carton under Head 1.
- Take the cursor to submenu ‘Reference Code’ with the help of up and down keys and delete the existing value by pressing the delete key.
- Check the pharmacode value from Standard Pack Specification for carton and feed the same as Reference code using Numeric keys. Press Enter key to save the setting.
- Press F3 key to program pharmacode. For example, Front Side Leaflet under Head 2.
- Take the cursor to submenu ‘Reference Code’ with the help of up and down keys and delete the existing value by pressing the delete key.
- Check the pharmacode value from Standard Pack Specification for leaflet and feed the same as Reference code using Numeric keys. Check the standard pack specification for mini code (if applicable), select the mini code and press Enter key to save the setting.
- Press F4 key to program pharmacode. For example, Aluminium foil / labels / second side of leaflet / tubes under Head 3.
- Take the cursor to submenu ‘Reference Code’ with the help of up and down keys and delete the existing value by pressing the delete key.
- Check the pharmacode value on Standard Pack Specification for Aluminium foil / label /second side of leaflet / tube and feed the same as Reference code using Numeric keys. Check the standard pack specification for mini code (if applicable), select the mini code and press Enter key to save the setting.
- Press F5 key to program pharmacode. For example, aluminium foil / labels / tubes under Head 4 (wherever applicable).
- Take the cursor to submenu ‘Reference Code’ with the help of up and down keys and delete the existing value by pressing the delete key
After programming for all the Heads switch over to Main menu by pressing F1 key. - Turn the key in anticlockwise direction to Run Mode and remove the key from the key slot.
- Handover the key to Production Head after setting.
-
Setting and Operation of Label Sensors:
- Set the cocam of pharmacode in horizontal or vertical direction as per the orientation of printed pharmacode on printed packing material.
- Then feed the pharmacode in the Argus system. Take one label in front of cocam. Go to head diagnosis and adjust the cocam in front of printed pharmacode and see that phrm is 100% and fix the cocam head and gate signal sensor.
- Cocam position should be fixed where label stoppage is observed and not at the position where the label pharmacode is in motion.
-
Setting and Operation of Booklet Scanner:
- Set the LLS Scanner of pharmacode reader to horizontal or vertical direction as per the orientation of printed pharmacode on the booklet.
- Feed the reference pharmacode value in the Argus system. Take one booklet in front of LLS.
- Go to ‘Head diagnosis’ and adjust the LLS in front of printed pharmacode and see that the phrm is 100% and fix the LLS and gate signal sensor.
-
Setting and Operation of Carton Sensor:
- Set the preoptic mirror of cosi221 / 2D cosi that it is between the two cartons when machine is in stop position.
- Set the cosi221 / 2D cosi beam so that it is at the centre of the pharmacode. Then feed the pharmacode value in Argus system as per standard pack specification using numeric keys.
- For laminated cartons with glossy finish on the pharmacode, the tolerance level is to be adjusted for effective pharmacode reading.
-
Setting and Operation of Leaflet Sensor:
- In case of cartonator, leaflet should be fed in the magazine with folded side facing the suction nozzle to avoid fluctuation during pharmacode reading.
- In case of cartonator, set the sensor on a cam at the back side of the leaflet folding unit for synchronization of the 2D-cosi scanner trigger with the cartonator speed.
- In case of unfolded leaflets the setting of Cosi 221 / 2D Cosi should be done in such a way that the beam of cosi221 / 2D Cosi should bisect the preprinted pharmacode.
- For reading second side of the leaflet, set the cosi221 / 2D Cosi sensor in such a way that the beam of cosi221 / 2D Cosi should bisect the preprinted pharmacode.
- Adjust the cosi221 beam so that it is just before pharmacode of the Leaflets when machine is in the stop position. The beam should be focused on the center of the pharmacode.
-
Setting and Operation of Foil Sensor:
- Adjust the reflector flap so that edge of the flap is just touching the pharmacode of the foil for effective pharmacode reading.
- Setting Operation of Tube Sensor:
- Set the cosi221 beam so that it is at the Centre of pharmacode.
- For glossy finish on the pharmacode, the tolerance level should be adjusted for efficient
pharmacode reading. - The position of the beam should be before and in the center of the pharmacode.
Note: Ensure that the machine on which the sensors are mounted are free from vibration and adequate measures are taken to avoid false reading of scanners.
-
Operation and In-process checks:
- Run the respective machine initially at the minimum possible speed and as applicable for the pharmacode reader.
- Ensure that pharmacode of all the items passes through or in front of the respective scanner.
- Verify the value displayed on the screen of system of the scanner and check against the Standard Pack Specification. The reading should match as given in specifications. Record the same in the Batch Packing Record.
-
Challenge procedure:
1.While adding a bar on the pharmacode of carton / label / foil / leaflet / tube / display carton / cards of card pack / booklet, put a cross mark on entire overprinting zone indicating as unusable item.
2. Challenge the pharmacode scanner by putting additional thin bar preferably at the end of the pharmacode or merge any two bars of pharmacode with pen on the carton, foil, label, leaflet and tube (wherever applicable).
3.In case of challenging the Data matrix code or 2D code put a thick dot on 2-D code by permanent black board marker.
4.Check for blister packing machine / cartonator/labeling machine/ conveyor stoppage indicated by the audio alarm or by the error message.
5.Check whether the challenged carton / foil / label / leaflet / tube / display carton / cards of card pack / booklet are rejected.
6.The machine should be started only after the same is acknowledged by Packing Officer.
7.Record the observation in Batch Packing Record. Pharmacode Challenged samples should be stored in the pharmacode rejection box/ rejection cage labeled as ‘rejects’.
8.Incase during in-process checks, if the functioning of pharmacode reader is found to be improper, then check manually all the packs packed in the previous interval. Inform Quality Assurance and Engineering and get it rectified. After rectification carry out in-process checks as per steps under point no. 1,2,3 and record the observations in Batch Packing Record.
9.Pharmacode challenged samples of carton / leaflet / foil / tube / label / cards of card pack /display carton / booklet should be destroyed at the end of the batch / end of the activity on the day and the same should be reconciled in the Batch Packing Record.
10.In case of Aluminium foil, remove the rejected pack after punching by blister pack machine onto the online conveyer and ensure that the same is put in rejection bin.
11.Carton/leaflet/label/booklet rejected for pharmacode defects or during in-process checks or machine run should be destroyed at the end of the batch/ at the end of the activity on the day and same should be reconciled in Batch Packing record.
Note :
a) Pharmacode is designed considering the movement of carton from left to right whereas for leaflet movement is from top to bottom in case of CAM cartonator and PAMPAC cartonator is left to right. For blister pack machine it should be right to left for aluminium foil / glassine foil. For labelling machine it should be from right to left. For tube filling machine it should be from left to right.
b) In case of packing material where pharmacode is not incorporated, this system can be bypassed.
c) If wrong pharmacode is detected with missing printed matter i.e. missing bar in pharmacode or mix-up of packing material, stop the activity immediately. Inform Quality Assurance and carry out necessary investigation.
d) Portable pharmacode reader can be used for scanning the pharmacode during initial proof checking and for in-process checks (As applicable).Portable LLS scanner needs to be configured for reading a particular type of code i.e. barcode/pharmacode/2D code before
verification against standard pharmacode, barcode, 2D code specimen. Record the observations in Specified format.
e) LLS Scanner cannot detect red colour bar from the printed pharmacode.
f) Wherever the red colour or light colour bars from the printed pharmacode are not scannable follow below steps :
- Replace the faulty Pharmacode reader with spare Pharmacode reader on packing line if available
- If spare Pharmacode reader is not available, then Pharmacode checking activity should be done offline on camera inspection system / Pharmacode Reader & counter verification to be done by QA officer.
- In case were Point No. 4 and 5 is not possible/applicable following manual activity should be performed by packing officer & verified by QA officer
- Flip checking should be done for each bundle / packet of packing material like labels, leaflets, cartons (inner / outer), catch covers, display carton, cards of card pack and booklets before loading the material on machine under supervision of packing officer and verification of QA officer. Attach the same with Batch Packing Record.
- Flip check should be done manually.
-
Action In case of System Failure:
- In case of system failure follow below mentioned procedure.
- Whenever Pharmacode reader stops reading the code, inform Department Head and Quality Assurance. Engineering Department should then be informed to get the fault rectified. When the pharmacode reader is not functioning or not available, 100% inspection of cartons, leaflets, and sheet form labels should be done before taking the same online for packing. Roll form labels should be checked after application. After rectification of the fault, challenge the system as per challenge procedure before starting the activity.
- If the fault cannot be resolved, inform the system supplier to rectify the fault.
- Replace the faulty Pharmacode reader with spare Pharmacode reader on packing line if available
- If spare Pharmacode reader is not available, then Pharmacode checking activity should be done offline on camera inspection system / Pharmacode Reader & counter verification to be done by QA officer.
- In case were Point No. 4 and 5 is not possible/applicable following manual activity should be performed by packing officer & verified by QA officer
- Flip checking should be done for each bundle / packet of packing material like labels, leaflets, cartons (inner / outer), catch covers, display carton, cards of card pack and booklets before loading the material on machine under supervision of packing officer and verification of QA officer. Attach the same with Batch Packing Record.
-
Flip check should be done as follows:
- Hold the bundle in one hand in such a manner that printed matter should be visible/readable and flip the complete bundle with the other hand. Record the observation in Specified Format.
- In the case of any mix ups / defects observed in the printed packing material, the activity should be stopped. All material should be quarantined and same should be informed to Department Head and Quality Assurance Department by mentioning the same in the remark
column and attach specimen sample (if any). - Packing Department and Quality Assurance should inspect and evaluate the mix up / defects in printed packing material and action plan should be made in consultation with Unit Quality Assurance Head and Packaging Head.
- Item code should be verified at start of the batch, every two hour, start of the day, after every
A.R. number change, change in roll (for label) and after restart of the batch if machine is idle for more than 30 minutes and the same should be recorded in Specified Format or in Batch Packing Record. Same should be verified by QA officer. - For sticker label, packing can be continued by checking item code after every two hour as in-process check and record the same in Batch Packing Record or specified Format.
- Manual scanners to check the barcode / pharmacode at initial, middle and end of the batch or
at initial and end of the batch in case the batch size is small and in case of change in A. R. No. and in case of consumption of EMCM should be used by Production Officer and verified by QA officer. The same should be recorded in specified Format. - Study exercise should be carried out for each type printed packing material like carton, foil, label, leaflet, tube, display carton, cards of card pack and booklet.
Annexures :
Annexure I : FLIP CHECKING FOR PACKING MATERIAL
Annexure II : BARCODE SCANNING RECORD
Annexure III : ITEM CODE VERIFICATION RECORD
Annexure I
FLIP CHECKING FOR PACKING MATERIAL
Product: ________________ Item : _________________
Batch No.: _______________ Code No.: ________________
Date | Flip check done on each pack | Done By
(Production ) |
Verified By
(Quality Assurance ) |
Remarks | |||||||||
Annexure II
BARCODE SCANNING RECORD
Date:___________ Product: ___________ B. No. :___________
First Barcode: _____________ Second Barcode: _________________
Item
Name |
Al. Foil | Inner Carton | Outer Carton | Scanned By
(Production) |
Verified By
(QA)
|
|||
Time
|
Bar Code-1 | Bar Code-2 | Bar Code-1 | Bar Code-2 | Bar Code-1 | Bar Code-2 | ||
Format III
ITEM CODE VERIFICATION RECORD
Product: ______________________________ B. No.: _______________
Item Name | Verified By
(Production) |
|||||
Time
|
Code No.: | Code No.: | Code No.: | Code No.: | Code No.: | |