Rapid Mixer Granulator operation and Working Principle
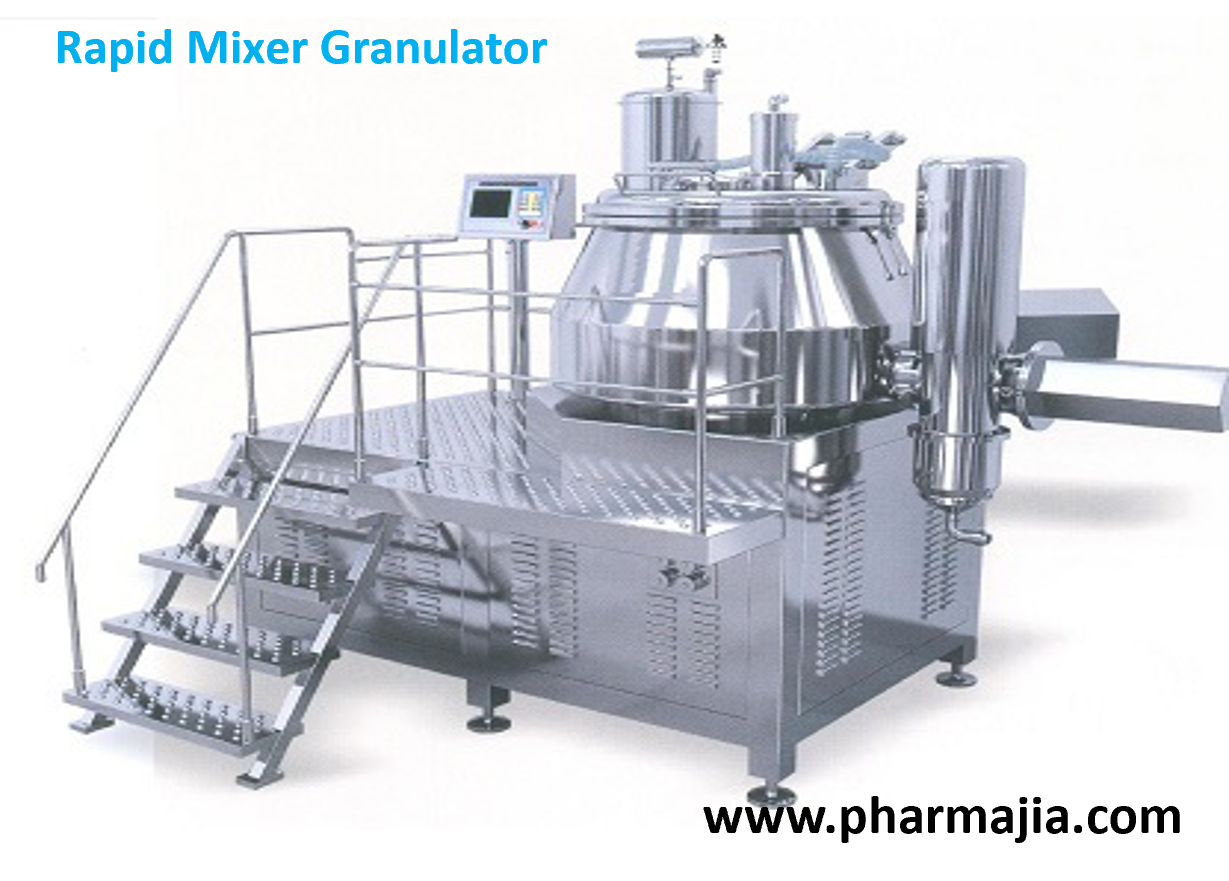
This article describes information about Rapid Mixer Granulator (RMG) and Its Working principle, advantages, disadvantages, comparisons and applications.
What is mean by Rapid Mixer Granulator (RMG) and Its Working ?
Rapid Mixer granulator is a pharmaceutical granulating equipment used for wet granulation processes. It is designed to produce uniform and dense granules of various sizes and shapes in a short period by using the mechanisms like shear, compaction and Impact. This equipment uses a combination of mechanical and hydraulic forces to mix and granulate the ingredients.
Initially dry powders added to the mixing chamber, where they are mixed with a binder solution. The mixing is done through impeller blades that rotate at high speeds, creating shear forces that break down the particles into smaller sizes. Binder solution is added in a controlled manner to form granules. Chopper is used to break the wet Lumps during granulations if observed during granulation. The granules are then discharged from the mixing chamber using a discharge port.
It is also termed as in different ways like High Speed mixer Granulator (HSMG), High Shear mixer Granulator (HSMG), Sizoner.
Components of Rapid Mixer Granulator
The Rapid mixer granulator consists of several components that work together to perform the mixing and granulation process. These components include:
- Mixing Bowl
- Impeller Blade
- Chopper Blades
- Discharge port
- Control panel
Mixing Bowl
The mixing bowl is the main component of the Rapid Mixer granulator, where the materials are mixed and granulated. It is made of stainless steel, which is easy to clean and maintain.
Impeller Blade :
The mixing impeller is a rotating blade that is used to mix the materials with the binder solution inside the mixing bowl. It is designed to create a high shear force, which breaks down the particles and produces a uniform wet mass/Blend.
Chopper Blade :
The chopper is a rotating blade that is used to break down the wet lumps into smaller ones, producing a uniform granule size. It is also used to prevent the formation of lumps and to remove air pockets from the granules.
Discharge Port :
The discharge port is located at the side bottom of the mixing bowl, and it is used to discharge the granules from the Rapid mixer granulator.
Control panel/HMI :
The control Panel/HMI is used to control the speed of the mixing impeller and the chopper, as well as other process parameters, such as temperature and time. It is designed to ensure that the granulation process is carried out efficiently and consistently.
Advantages of Rapid Mixer Granulator
It has numerous advantages , Some of these advantages enlisted are as below :
- High efficiency and productivity
- Uniform and dense granules
- Short mixing and granulation time
- Easy scale-up and process validation
- Minimal dust emission
- Reduced operator exposure to hazardous materials
Disadvantages of Rapid Mixer Granulator.
In spite of its numerous advantages, it is also has some Disadvantages are as below
- High initial cost
- High maintenance cost
- Limited flexibility for processing different materials
- Possibility of over-granulation or under-granulation
- Limited capacity for large-scale production
Comparison of Rapid Mixer Granulator with Other available Granulating Equipment ?
The Rapid Mixer Granulator has several advantages over other mixing equipment, such as:
- Fluid bed processor: The Rapid Mixer granulator produces denser and more uniform granules than fluid bed processor.
- Planetary mixer: The Rapid Mixer granulator is more efficient and produces better granules than planetary mixer.
Applications of Rapid Mixer Granulator
The Rapid Mixer Granulator is widely used in pharmaceutical manufacturing for Granulating the powder material for the usage in Tablet, Capsule etc.
How to choose Right Rapid Mixer Granulator ?
Several Granulators available in the market, it is very tough task to choose the right equipment for granulation. However there are some factors that can be considered to make an informed decision before procurement.
- Production capacity
- Materials of construction
- Impeller speed
- Chopper speed
- Temperature Control option
- Control panel.
Frequently asked questions (FAQs)
What safety precautions are necessary when using an RMG?
Operators must be trained, safety guards should be in place, and standard operating procedures must be followed to ensure safety.
Are there different sizes and configurations of RMGs available?
Yes, RMGs come in various sizes and configurations for different production capacities.
Are RMGs handle materials with different flow properties and densities?
Yes, with proper adjustments, RMGs can handle a wide range of materials.
What are some common challenges in maintaining temperature control during granulation in an RMG?
Temperature control can be challenging due to the heat generated during high-speed mixing; efficient cooling and monitoring are essential.
Can RMGs be used for continuous granulation processes?
Yes, some RMGs can be adapted for continuous granulation, enhancing efficiency and productivity.
What are some safety features that should be present in an RMG to protect operators and prevent accidents?
Safety interlocks, emergency stop buttons, and protective covers are common safety features are available in RMG
Can RMGs be used for granulating materials that require controlled release formulations?
Yes, RMGs can be used for controlled release granulation by adjusting process parameters and usage of suitable material.
What is the purpose of the control panel in an RMG, and how is it used to control the process?
The control panel allows operators to set and monitor various process parameters, such as mixing time, Chopper and impeller speed.
How is the moisture content of granules controlled during the granulation process in an RMG?
By adjusting the liquid binder addition rate and monitoring granule characteristics.
Are there any specific measures to prevent dust and contamination in the air during RMG operation?
Proper containment systems and dust extraction are used to prevent contamination.