SOP on Good Laboratory Practices
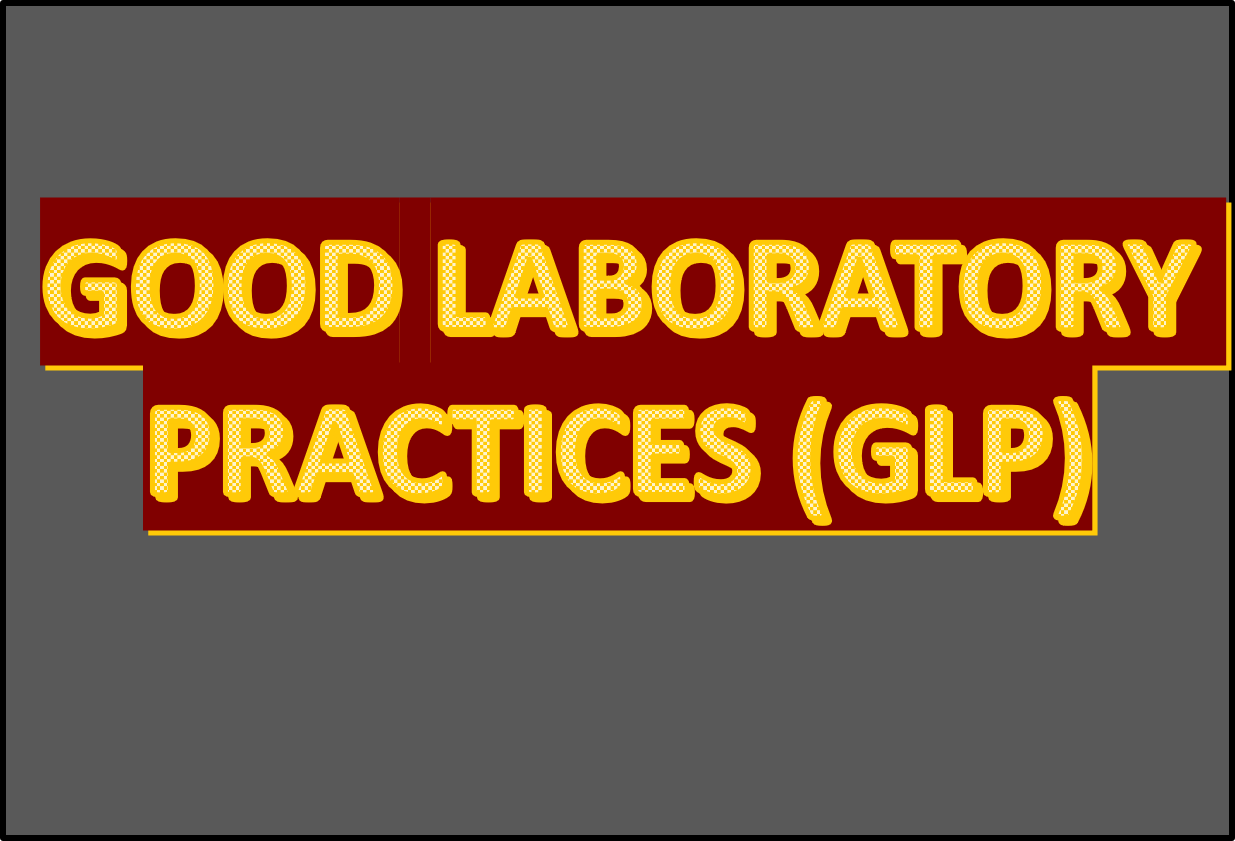
It describes the (Standard Operating procedure) SOP on Good Laboratory Practices (GLP) in laboratories of Pharmaceutical Industry.
SOP on Good Laboratory Practices
I. Purpose & Scope:
- To provide a general methodology to be followed Good Laboratory Practices during working in Quality control laboratory in pharmaceutical industry
- Applicable to all personnel who are working in Quality control laboratory.
II. Responsibilities:
• All Quality Control and related personnel shall be responsible to follow and implement this SOP.
III : Introduction and Procedural Part :
Definition :
Good Laboratory Practices (GLP) in the pharmaceutical industry refer to a set of guidelines and standards that ensure the quality, integrity, and reliability of laboratory studies and data generated during the development and testing of pharmaceutical products. GLP encompasses various aspects of laboratory operations, including personnel, facilities, equipment, documentation, sample handling, data recording, and reporting. These practices are designed to minimize errors, promote accuracy, and maintain consistency in laboratory procedures, ultimately ensuring the safety and efficacy of pharmaceutical products.
1) MAIN OBJECTIVE OF GOOD LABORATORY PRACTICES INCLUDE :
- Standardization: GLP aims to standardize laboratory procedures, ensuring that experiments are conducted consistently and reproducibly across different laboratories. This helps to minimize variations in results and allows for better comparison and interpretation of data.
- Quality Assurance: GLP emphasizes the implementation of quality control measures to ensure accuracy, precision, and reliability of experimental data. This involves appropriate calibration and maintenance of equipment, validation of analytical methods, and proper handling and storage of samples and reagents.
- Personnel Training: GLP emphasizes the training and competency assessment of laboratory personnel. It ensures that individuals involved in conducting experiments are adequately trained and possess the necessary knowledge and skills to perform their tasks accurately and safely.
- Documentation: GLP requires the comprehensive documentation of all laboratory activities, including experimental protocols, procedures, observations, and results. Proper documentation allows for traceability, transparency, and reproducibility of experiments, facilitating data verification and regulatory compliance.
- Facilities and Equipment: GLP mandates that laboratories have suitable facilities and equipment to support the conduct of experiments. This includes appropriate laboratory infrastructure, well-maintained instruments, and controlled environmental conditions to prevent contamination or interference with the experimental process.
- Data Integrity: GLP emphasizes the integrity and confidentiality of data generated during experiments. It requires proper data management, including secure storage, backup, and protection against unauthorized access or manipulation.
- Compliance and Auditing: GLP promotes adherence to applicable regulations and guidelines governing laboratory practices. Regular internal and external audits are conducted to ensure compliance and identify areas for improvement.
2) FUNDAMENTAL RULES TO BE FOLLOWED IN LABORATORY INCLUDEDS :
- Make sure to have the correct written instructions before starting a task.
- Do not carry out any task for which you have not been trained.
- Always follow instructions precisely, If in any doubt, ask.
- Keep records of information, results and actions taken. Make clear accurate records of what was done.
- Before using the any instrument/equipment/Glasswares should be clean, calibrated and correct ones as per procedure.
- Always notify if labels are seen either detached or appear to incorrect or are in wrong place.
- Report any labels that are damaged or dirty.
- Never remove a label which has been incorrectly applied and never stick a new label over an old one of the same type.
- If label is incorrectly affixed strike it off, sign and paste new correct label adjacent to it.
- Keep everything clean and tidy.
- Quality control laboratory and work benches should keep clean in accordance with written cleaning schedules.
- Clean the glassware, drying oven, refrigerator, walk in chamber, incubators, water bath ,dissolution tester, disintegration testers etc, used in the quality control laboratory as per the procedure.
- Clean the work benches after completion of work or at the end of the day whichever is earlier and keep the respective specification, SOP’s etc. used back to the designated place.
- While closing the Quality Control Laboratory, ensure that all water taps, instruments (which are not running), equipment’s, computers are put ‘OFF’. Put off the lights, AC’s and closes the department.
- The laboratory main door should be locked and keys should be submitted to concern person.
- All glassware in used for analysis shall be properly labelled to indicate sample details. Glassware can be labelled with glass marker pen or proper sticker label.
3) LABORATORY PREMISES :
- Maintain the laboratory and its premises clean and tidy.
- Quality Control personnel should avoid mix-ups and cross contamination during analysis.
- During analysis of potent molecules wear disposable gowns and necessary safety utilities.
- The disposable gowns shall be disposed after analysis in separate used garment bin.
- Dedicated glassware’s shall be used for the analysis of potent Molecules.
- The Glassware used for potent molecules are kept at designated place and shall not be used for another product.
- Contaminated Glassware’s of potent molecules shall be cleaned, dried and stored as per respective SOP.
- Keep work benches of laboratories clean and tidy all the time.
- Keep the samples, standards, laboratory reagent, apparatus, accessories and records at adequate and suitable storage space.
- For analytical preparation wherever water is to be used shall be use as ‘purified water’ and for chromatographic analysis like HPLC, GC, etc. use HPLC grade water or water generated by any purification system.
- The utilities like compressed air, vacuum required for the functioning of laboratory shall have identification mark.
- Maintain temperature record in quality control department as per SOP Operation & calibration of Hygrometer, the temperature in Quality Control Department shall be controlled and the limit is not more than 25°C.
- The Air Conditioner shall be set at 23°C in Quality Control Department.
- Follow the procedure in case access control system is to be followed where restricted entry is necessary. The area should be labelled appropriately as per operation for better control.
- In case of hazardous and poisonous materials, keep it at adequate storage area/facility with lock and key to avoid misuse. Also keep reserve sample, stability sample, laboratory standards in lock and key.
- Use eye washer, water shower, first aid kit etc. in case of emergency which may arise during operation. Always identify the location of emergency exit in the laboratory for exit during emergency.
4) PERSONNEL:
- Personnel suffering from an infectious disease or having open lesion on the exposed surface of the body should not engage in activities that could results in compromising the quality of analysis.
- All employees shall be instructed to report about their illness or abnormal health condition to their immediate supervisor so that appropriate action can be taken.
- The job responsibility should be assigned according to competency of the person and it should be timely revised for addition or deletion of responsibilities assigned previously.
- Personnel should practice good sanitization and health habits.
- Smoking, eating drinking, chilling or keeping plants, food, drinks and personnel medicine should not be permitted in laboratories area, where they might adversely influence the product quality.
- Personnel should wear clean clothing (company uniform) suitable for activity with which they are involved and this clothing should be changed when appropriate. Personnel should strictly follow entry/exit and gowning procedure.
- While handling hazardous chemicals and procedure of change of clothing and use of personnel protective equipment’s and safety appliances should be strictly followed.
- Never handle any chemicals, raw materials intermediate or finished, unpacked product with bare hands. Always use the appropriate hand gloves while handling the same.
- All personnel should follow the time schedule with respect to shift and should be punctual in attendance.
5) TRAINING:
- Training should be regularly conducted by qualified individuals and should cover, at a minimum, the particular operation that the employee performs.
- Training should be given on both theory and practical of the work being undertaken in a particular area, as well as relevant ‘on-job’ (i.e. Task-based) training.
- Records of training must be maintained. Training should be periodically accessed.
- All staff, including new staff and existing staff shall be undergo basic training on Good Laboratory Practices during induction and at regular intervals subsequently. This training programme should be periodically updated.
6) INSTRUMENTS / EQUIPMENT’S / ACCESSORIES :
- The analytical instrument shall be house in dust free environment and whenever required, conditions of temperature and humidity shall be maintained at periodic checks of temperature and humidity shall be made and recorded.
- All instruments / Equipment’s shall be qualified properly through IQ, OQ and PQ activities after receive in the Laboratory.
- The instruments, instrument bench and surrounding areas shall be kept clean, tidy and free from vibration at all times.
- Instruments requiring calibration shall be calibrated at regular intervals and records of such calibration or maintenance be maintained and there shall be written instruction in the form of Standard operating procedures for the operation.
- Other equipment / accessory such as thermometers, weight boxes, etc. shall be thoroughly checked for accuracy of calibration before acceptance for use and accessory such as burette, pipette, volumetric flask should be used as Class A grade with certificate.
- Standard operating procedure should be displayed near each instrument / equipment and should be followed whenever used.
- The instruments / equipment’s should be used within the permitted range and as per the written operating procedures.
- To the extent possible switch off all equipment’s after use at the end of the day.
- While performing analysis on instrument, display the ‘analysis status’ indicating details of ongoing analysis.
- List of ‘Authorized Users’ for all major instruments should be displayed as per Respective SOP format update all relevant usage logbooks concurrently when analysis is being carried out.
- Usage log should be maintained for usage record of instruments / equipment’s as per respective SOP.
- Individual column usage log for HPLC columns should be maintained as per respective SOP No. i.e. Procedure for receipt, Storage, performance, regeneration & destruction of HPLC columns.
- Temperature and humidity of stability Incubators should be maintained as per requirement and data should be recorded as per the written procedure as per Respective SOP i.e. Stability Studies.
- All the desiccators used in the laboratory should contain sufficient quantity of suitable desiccant. The desiccant should be replaced weekly or when desiccant losses its effectiveness (from blue to white or pink) whichever is earlier, update the label of the desiccators; also maintain the record of desiccant replacement.
- Water from Instrument / equipment (e.g. Dissolution, Sonicators, etc.) shall be changed regularly and status label shall be updated.
When Instrument / equipment is not in use for longer period (e.g. breakdown) water should be removed and the Instrument / Equipment kept dry. - Working involving the evolution of harmful Vapours shall be carried out in a fume cupboard. There should be a water drainage system inside the fume cupboard and shall be checked frequently to ensure that there is no water clogging and it is in order.
- The wash bottles used for cleaning of electrodes and other work should bear “Purified Water” label and affix the label. The water in the bottle should be changed daily or when get emptied. At the end of day’s operation or after use, Instrument / equipment should be cleaned and switched off and kept covered wherever possible.
7) COMPUTERIZED SYSTEMS:
- Computerized systems should have sufficient controls to prevent unauthorized access or changes to data. Software should not be left opened and unattended to avoid misuse.
- After use, save the data and close all operating system properly and then switch off the computer system.
- To operate the computer system with instruments, refer concerned instrument operating procedure.
- For documentation purpose, use to suitable operating system like MS word, excel etc. The major documents prepared like specifications, SOPs etc. using the MS word, excel should have the password protection.
8) TESTING AND REPORTING :
- Testing should be conducted under the supervision of competent technical staff.
- There should be written procedure for testing materials and products at different stage of manufacture, describing the methods and instruments / equipment’s to be used.
- All samples for analysis should be registered and numbered for easy retrieval of samples and records related to them. The Specification should be available for every product / item.
- Testing should be done as per approved specification. The results obtained should be checked for compliance against specification. All calculations should be checked. The records of testing should be maintained.
- During chromatographic analysis, use blank determinations at appropriate intervals to confirm and ensure baseline stability verification and carry over contaminations.
- To determine the LOD / Water content for products / materials where Assay need to be calculated on dried or anhydrous basis.
Use clean spatulas or butter papers for transferring and weighing samples. - Attach all relevant analytical raw data obtained from instruments such as Analytical Balances, High Performance Liquid Chromatograph, UV-Spectrophotometer, IR-Spectrophotometer, Polarimeter, Refractometer, Potentiometer and Bulk Density Apparatus to the record of analysis/ calculation sheet after labelling the same.
- While performing tests, instructions for use and storage of Laboratory reagents, volumetric solutions, reference standards etc. should be followed.
- Do not leave any blank space on page after completion of document or calculation. Blank space should be strike off by cross line by written remark as NA’ with sign and date.
- In case of analysis of temperature sensitive material and standards stored at 2 to 8°C or in freezer (between – 25°C to – 10°C), follow the procedure as below.
- Collect the sample from respective storage area and allow the same to attain the ambient temperature before using i.e. weighing, pipetting etc.
- Do not expose the sample to ambient temperature for longer duration i.e. for greater than 60 minutes.
- During analysis close the sample container immediately after use and do not leave it opened. Preserve the sample container away from heat. Replace sample back to storage area immediately after sample preparation.
- The test record should include name of material / product with dosage form wherever applicable, batch number, reference to the relevant specification and testing procedure, test results, including observations and calculations, date of testing, initials of persons performing testing, initials of persons verifying the testing and calculations, a clear statement of release or rejection (or other status decision) and dated signature of the designated responsible personnel should be available.
- In case of the chromatographic analysis like HPLC, mobile phase prepared should be properly labelled. Label should indicate Mobile phase should be valid up to 24 hrs to 48 hrs if not mentioned in standard test procedure.
- After completion of analysis and review of data, glassware should be cleared from the workbench. Discard the contents from glassware and keep it for washing.
- The disposal of waste material, broken glassware if any and balance analytical samples should be done carefully and according to procedure.
- Certification of analysis should be prepared for required consignment.
- The certificate should list each test performed in accordance with specification, including the acceptance limits and results obtained.
During analysis, if any abnormal or unexpected event or out of specification results occurs, address the same using an deviation Report or out of specification report. - Analysts shall report all deviations and OOS to the Supervisor or QC Manager as soon as possible.
- Record the Refrigerator temperature record at Being of Shift and End of Shift as per respective SOP format.
9) CHEMICALS, REAGENTS, GLASSWARE AND ANALYTICAL STANDARDS :
- Special attention should be given to the quality of laboratory reagents, volumetric glassware and solutions, standards, and culture media. Reagents and standards should be prepared and labelled as per the written procedures. For chromatographic analysis like HPLC and GC, always use chromatographic grade solvents and reagents.
- All reagents and solutions in the laboratory shall be properly identified with a label. Validity should be provided as appropriate for analytical reagents or standard solutions prepared and should be indicated on label together with specific storage conditions.
Check the validity period of chemicals before use. Discard all expired chemicals and reagents. - Adequate space with proper storage condition in the laboratory shall be provided for keeping reference and working standards and be maintained by the quality control department.
- The standards and solutions should be labelled.
- Storage and handling of chemicals and reagents shall be done in a manner considering the physicochemical properties of these substances and the hazards involved in their use.
- All the solutions, solvents dispensed and solvent waste collected in vessel / beaker should be covered entirely with appropriate cover e.g. using aluminium foil / glass lead etc. to avoid the probable contamination as well as exposure of the solvent Vapours in the laboratory.
- The glassware used for analysis should be of appropriate quality and capacity. Only Class A graduated glassware should be used unless validated. Certificate of calibration should be maintained. Graduated glassware should not be dried at high temperature (generally more than 60°C) which could alter volumetric graduation.
- Dedicated glassware’s shall be used for the analysis of potent Molecules.
- All glassware in use shall be labelled properly . Glassware can be labelled with glass marker pen or proper sticker label.
- The glassware should be examined before use for cleanliness and damage; do not use cracked, chipped or any other defective Glassware.
- Reference standard should be used minimum quantity for standard preparation by without changing concentration of the solution. If working standard/impurity standard is not sufficient in stock or received from outside vender, use this standard as a minimum quantity for preparation of standard solution by without changing concentration of the solution.
10) DOCUMENTATIONS:
- Specifications, instructions, procedures and records must be free from errors and available in writing.
- Documents should be approved, signed and dated by appropriate and authorized persons. Strict adherence to documented procedures and specifications should be ensured.
- Documents should be regularly reviewed and kept up-to-date.
- Circle the desired option, when multiple options are provided, unless specified otherwise.
- Any correction to a record should be scored with a single line and new entry should be made alongside the original entry, should be signed and dated, the correction should permit the reading of the original information There should be no overwriting and correction fluid/ eraser should not be used.
- Records should be made or completed at the time each action is taken and in such a way that all significant activities are traceable Document should be preserved appropriately (Product / Material wise or AR NO. wise) for easy retrieval and for appropriate time.
11) STABILITY STUDIES :
- Stability studies should be carried out to obtain evidence on how the quality of a drug substance or drug product varies with time under the influence of factors such as temperature, humidity and light and enables establishment of recommended storage conditions, retest periods or shelf life for drug substances or drug products.
- The test procedures used in stability testing should be stability indicative.
- A schedule should be designed to monitor the stability of each product.
- Out of specification or significant a typical trend should be investigated. Product failures should be promptly reported to technical head, regulatory affairs, R and D, quality assurance and customer, (if applicable), for necessary action.
- The possible impact on the batches distributed in the market should be considered. A summary of data generated should be written and maintained.