Equipment Calibration – In Pharmaceutical industry.
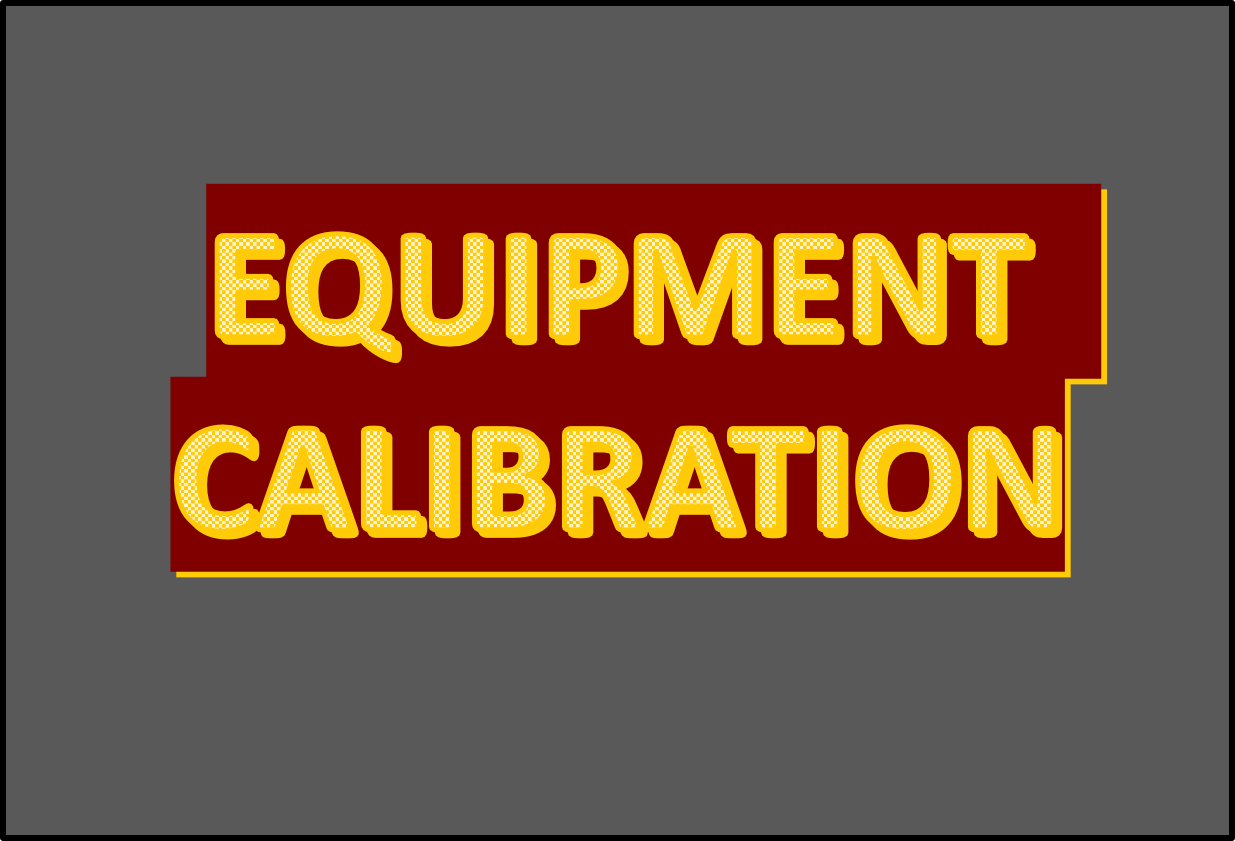
This article explains the detailing on Equipment calibration and Instruments used for calibration of equipment which is used in pharmaceutical industry.
EQUIPMENT CALIBRATION
What is mean by Equipment Calibration:
Why Equipment Calibration is Required :
If Equipment Calibration Found out of specification which steps should be Followed :
Importance of Equipment calibration in Manufacturing/Packing Operations :
Equipment Calibration plays a major role during operations in avoiding the production of inaccurate output, so the advantages of calibration for your machinery and measuring equipment cannot be overstated. There are several facets of calibration in manufacturing but in general, calibration is important in these two key areas:
- Calibration for measuring equipment ensures that your quality control processes are accurate and that will produce the Quality acceptable products and those are not accepting that should be rejected.
- Calibration for manufacturing machines creates a more efficient process by ensuring that equipment is operating as expected. Improperly calibrated or out of calibration equipment’s may results unpredictable manufacturing results and inaccurate products.
Reason why calibrations of Equipment’s are important:
Accuracy: The most important reason that accuracy is a critical standard in manufacturing operations is quality, safety and efficacy of the finished products. Imprecise parts those outside of the required tolerance cannot be used because the likelihood of them functioning properly is very low.
In addition to above, inaccurately manufactured products caused by uncalibrated machinery can result in the following:
High rates of product rejection — Improperly calibrated machinery creates inefficiencies in qualitative production output and may results in bad Quality Product . If your quality control processes don’t reject Such products, your customers surely will and may results the market product Recall will cause huge cost incur to manufacturer.
Cost and Time overshoot — High numbers of rejected products will require additional production to replace them then these requirements will extend production time and threaten deadlines. They will also add process/production costs that cannot be passed on to the customer.
Reputation damage — Unhappy customers may leave poor reviews about your services, putting your brand and your pipeline of new customers in danger. In addition to that will impact on repeat orders.
Different Types of Instruments used in production area for equipment calibration in pharmaceutical Industry as below :
Instruments used for Calibrations. | ||
Sr. No. | Test Name | Instrument used |
1 | RPM Calibration | Tachometer |
2 | Noise Level | DB Meter/Decibel Meter |
3 | CFM Calibration | Anemometer |
4 | Light intensity | Lux meter |
5 | Temperature | Thermometer |
6 | Viscosity | Viscometer |
Need of Equipment Calibration
Calibration of equipment is not just desirable, it is rather a necessity. All measuring instruments, whether they are used in factories or laboratories need to be calibrated on a periodic basis to ensure they are offering accurate results. However, in factories and laboratories, measurement results are usually of a critical value. Deviation from accuracy can not only affect productivity but also cause threat to the life of workers. Hence, it is imperative that instrument calibration be carried out carefully and at regular intervals.