Top 69 FAQs on Tablet Granulations – For Beginners.
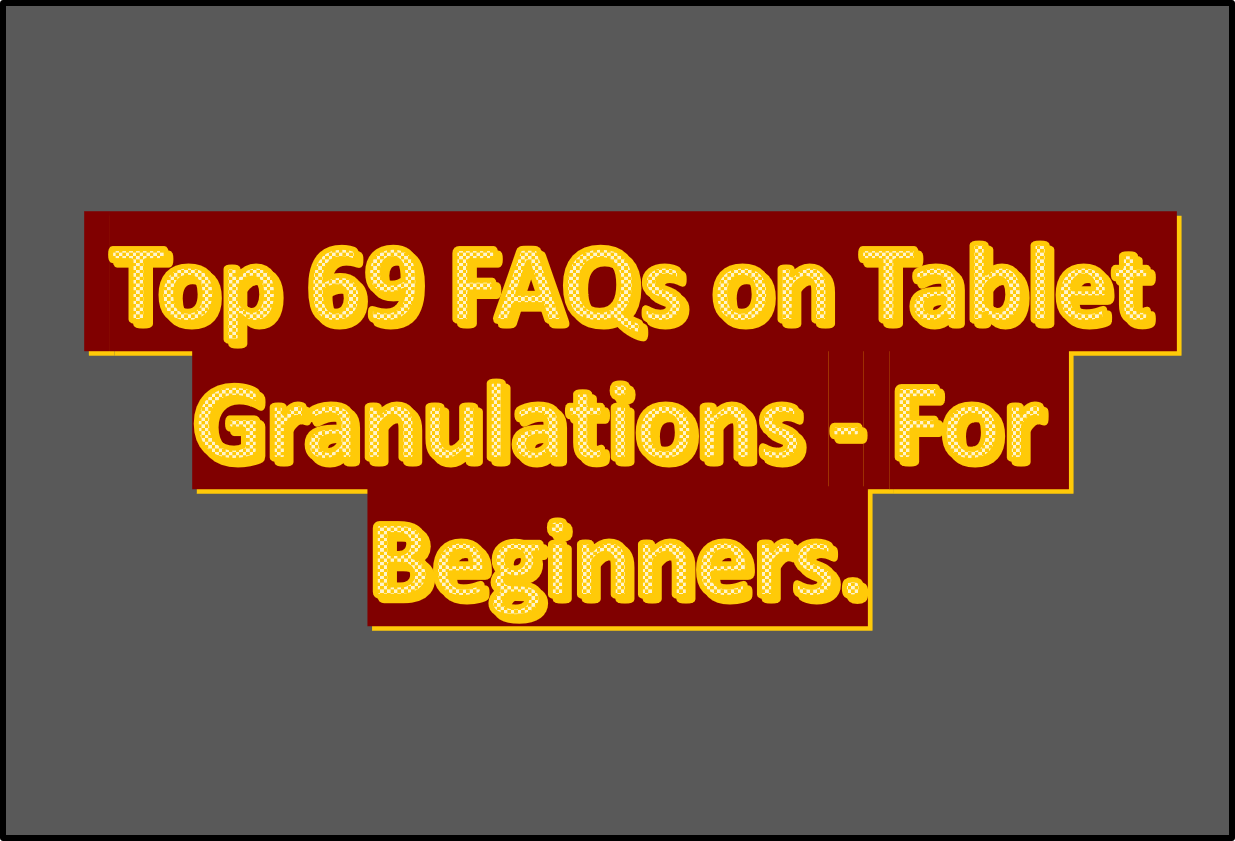
FAQs on Tablet Granulation
It includes Top 69 Frequently asked Questions with answers FAQs on Tablet Granulations for Pharmaceutical Products – For Beginners :
(Frequently asked Questions) FAQs on Tablet Granulations for Pharmaceutical Products – It’s for Beginners :
- What is Granulation?
Tablet Granulation is a process used in the pharmaceutical industry to transform fine powders into larger granules with improved flowability, compressibility, and uniformity. - What are the types of granulation?
There are two types of granulation: wet granulation and dry granulation. - What is wet granulation?
Wet granulation is a process in which the powder mixture is mixed with a liquid binder to form granules. - What is dry granulation?
Dry granulation is a process in which the powder mixture is compacted and then broken down into granules. - What are the advantages of wet granulation?
Wet granulation can improve the flowability, compressibility, and uniformity of the granules. It can also enhance the bioavailability of the active pharmaceutical ingredient. - What is the difference between wet granulation and dry granulation?
Wet granulation involves the use of a liquid binder to agglomerate the powder particles, while dry granulation involves the use of compression to form granules without the use of a liquid binder. - What are the disadvantages of wet granulation?
Wet granulation is a time-consuming and expensive process. It also requires the use of a liquid binder, which can affect the stability of the active pharmaceutical ingredient. - What are the advantages of dry granulation?
Dry granulation is a faster and more cost-effective process than wet granulation. It also preserves the stability of the active pharmaceutical ingredient. - What are the disadvantages of dry granulation?
Dry granulation can produce less uniform and less compressible granules than wet granulation will results Flow problem and weight variation issue during compression. - What is the granulation process flow?
The Tablet granulation process flow includes Sifting, Dry Mixing, Granulation, Drying, Milling, Sieving, Blending and Lubrication. - What is Sifting ?
It is commonly called as security Sifting. Security sifting is a process used to remove any foreign particles or contaminants from a granular mixture before further processing. - What is Dry Mixing ?
Dry Mixing is the process of Granulation in which homogenous powder mixture will create with active pharmaceutical ingredient and excipients. - What is granulation?
Granulation is the process of transforming the powder mixture into granules. - What is drying?
Drying is the process of removing the liquid binder from the granules. - What is milling ?
Milling is the process of cutting the large granules in to small uniform sizes. - What is sieving?
Sieving is the process of separating the granules by size. - What is blending?
Blending is the process of combining multiple ingredients, typically in powder or granular form, to create a homogenous mixture. - What is lubrication?
Lubrication is the process in which addition of a small amount of lubricant to a granular mixture to reduce friction and prevent particles from sticking together during the compression process in tablet manufacturing. - What are the common excipients used in granulation?
The common excipients used in Tablet granulation include binders, fillers, lubricants, Glidants disintegrants etc. In addition to that some of the specialized excipients used in the tablet granulation as per the specific requirement of formulations like colorants, Preservatives, Flavors, Antioxidants, Buffering agent, solublisers. - What is the role of binders in wet granulation?
The role of binders in wet granulation is to promote adhesion between the particles and form granules. - What are the common binders used in wet granulation?
The common binders used in wet granulation include water, Solvents (Ethanol, IPA), Starch, Hydroxy propyl methyl cellulose (HPMC) and polyvinylpyrrolidone (PVP). - What is the role of fillers in granulation?
The role of fillers in granulation is to provide bulk to the tablets and improve their physical characteristics such as hardness, friability, and disintegration time. - What are the common fillers used in granulation?
The common fillers used in tablet granulation include lactose, microcrystalline cellulose, and dibasic calcium phosphate. - What is the role of lubricants in granulation?
The role of lubricants in tablet granulation is to reduce friction between the granules and the tablet press, which improves flowability and prevents sticking. - What are the common lubricants used in granulation?
The common lubricants used in tablet granulation include magnesium stearate, stearic acid, and sodium stearyl fumarate. - What is the role of disintegrants in granulation?
The role of disintegrants in granulation is to promote the breakup of the tablet into small particles in the presence of water. - What are the common disintegrants used in granulation?
The common disintegrants used in granulation include croscarmellose sodium, sodium starch glycolate, and microcrystalline cellulose. - What is the role of glidants in granulation?
The role of glidants in granulation is to improve flowability and prevent sticking of the granules. - What are the common glidants used in granulation?
The common glidants used in granulation include colloidal silicon dioxide and talc. - What is the role of colorants in granulation?
The role of colorants in granulation is to provide visual identification of the tablets. - What are the common colorants used in granulation?
The common colorants used in granulation include iron oxides, titanium dioxide, and FD&C colors. - What is the role of flavors in granulation?
The role of flavors in granulation is to improve the taste of the tablets. - What are the common flavors used in granulation?
The common flavors used in granulation include natural and artificial flavors such as mint, fruit, and vanilla. - What is the role of preservatives in granulation?
The role of preservatives in granulation is to prevent microbial growth and extend the shelf life of the tablets. - What are the common preservatives used in granulation?
The common preservatives used in granulation include benzoic acid, sodium benzoate, and sorbic acid. - What is the role of antioxidants in granulation?
The role of antioxidants in granulation is to prevent degradation of the active ingredients and improve the stability of the tablets. - What are the common antioxidants used in granulation?
The common antioxidants used in granulation include ascorbic acid, tocopherol, and butylated hydroxy anisole (BHA). - What is the role of buffering agents in granulation?
The role of buffering agents in granulation is to maintain the pH of the tablets within a specific range, which can improve the stability and bioavailability of the active ingredients. - What are the common buffering agents used in granulation?
The common buffering agents used in granulation include citric acid, sodium bicarbonate, and potassium phosphate. - What is the role of solubilizers in granulation?
The role of solubilizers in granulation is to increase the solubility of poorly soluble active ingredients and improve their bioavailability. - What are the common solubilizers used in granulation?
The common solubilizers used in granulation include cyclodextrins, surfactants, and co-solvents. - What is a tablet?
A tablet is a solid dosage form that is made by compressing granules. - What is a capsule?
A capsule is a solid dosage form that is made by filling the Granules (API+ Excipients) into a gelatin shell. - What are the factors affecting granulation?
The factors affecting granulation include the properties of the active pharmaceutical ingredient and excipients, type of granulation process, equipment used and process parameters. - What are the process parameters of granulation?
The process parameters of granulation include the mixing time, mixing speed, binder concentration, drying temperature, drying time, Blending Time, Lubrication Time etc. - What are the equipments used in granulation process?
The common granulation equipment include Sifters, granulators, dryers, Mills, sifter, Blender. - What are the different types of blenders used in granulation?
The different types of Blenders used in granulation include V-Blender, Bin Blender, Double cone Blender, Octagonal Blender. - What are the different types of granulators used in granulation?
The different types of granulators used in tablet granulation include fluid bed granulators, high-shear mixer granulators. - What are the different types of dryers used in granulation?
The different types of dryers used in tablet granulation include fluid bed dryers, tray dryers, and vacuum dryers. - What is a fluid bed granulator?
A fluid bed granulator is a type of granulator that uses air to fluidize the powder mixture and spray the liquid binder solution on powder which transform it into granules. - What is a high-shear granulator?
A high-shear granulator is a type of granulator that uses to mix the powder mixture and transform it into granules. - What are the common methods used to evaluate the quality of granules?
The common methods used to evaluate the quality of granules include particle size analysis, Bulk Density and Tapped Density and moisture content analysis. - What is particle size analysis?
Particle size analysis is the process of measuring the size distribution of the granules by using the predefined sieves. - What is Bulk Density?
Bulk density is a measure of the mass of a powder or granular material per unit volume. It is commonly expressed in g/ml or kg/m³. Accurate measurement of bulk density helps optimize manufacturing processes and predicting flow behavior of a material. - What is Tapped Density?
Tapped density is a measure of the density of a powder or granular material when it has been settled and compacted under specific tapping conditions. It is typically expressed in g/ml or kg/m³. - What is moisture content analysis?
Moisture content analysis is the process of measuring the amount of moisture in the granules. - What is the purpose of evaluating the quality of granules?
The purpose of evaluating the quality of granules is to ensure that they meet the required specifications for their intended use. - What are the common problems encountered in granulation?
The common problems encountered in granulation include poor flowability, poor compressibility, segregation etc. - What is poor flowability?
Poor flowability is the inability of the granules to flow through the tablet press properly. - What is poor compressibility?
Poor compressibility is the inability of the granules to be compressed into tablets properly. - What is segregation?
Segregation is the separation of the granules by size or density. - What are the factors that can cause poor granule quality?
The factors that can cause poor granule quality include incorrect process parameters, poor equipment performance, and poor material quality. - What are the quality control measures in granulation?
The quality control measures in granulation include in-process testing like particle size analysis, Bulk density, Tapped Density and Loss on Drying or moisture content and Furthermore bulk testing done at Quality control Laboratory like Blend Uniformity and Assay of granules. - What is in-process testing?
In-process testing is the testing of the granules during the granulation process to ensure that they meet the required specifications. - What is Bulk product testing?
Bulk product testing is the testing at semifinished stage of product to ensure that it meets the required specifications. - Why is it important to maintain granulation equipment?
It is important to maintain granulation equipment to ensure that it operates efficiently and produces high-quality granules. - What are the common cleaning methods for granulation equipment?
The Two common cleaning methods for granulation equipment include dry cleaning and wet cleaning. - What is the purpose of cleaning granulation equipment?
The purpose of cleaning granulation equipment is to prevent contamination and cross-contamination of the granules. - What are the common causes of cross-contamination in granulation?
The common causes of cross-contamination in granulation include improper cleaning, improper handling of materials, and poor facility design.