What is mean by Dwell Time in Compression
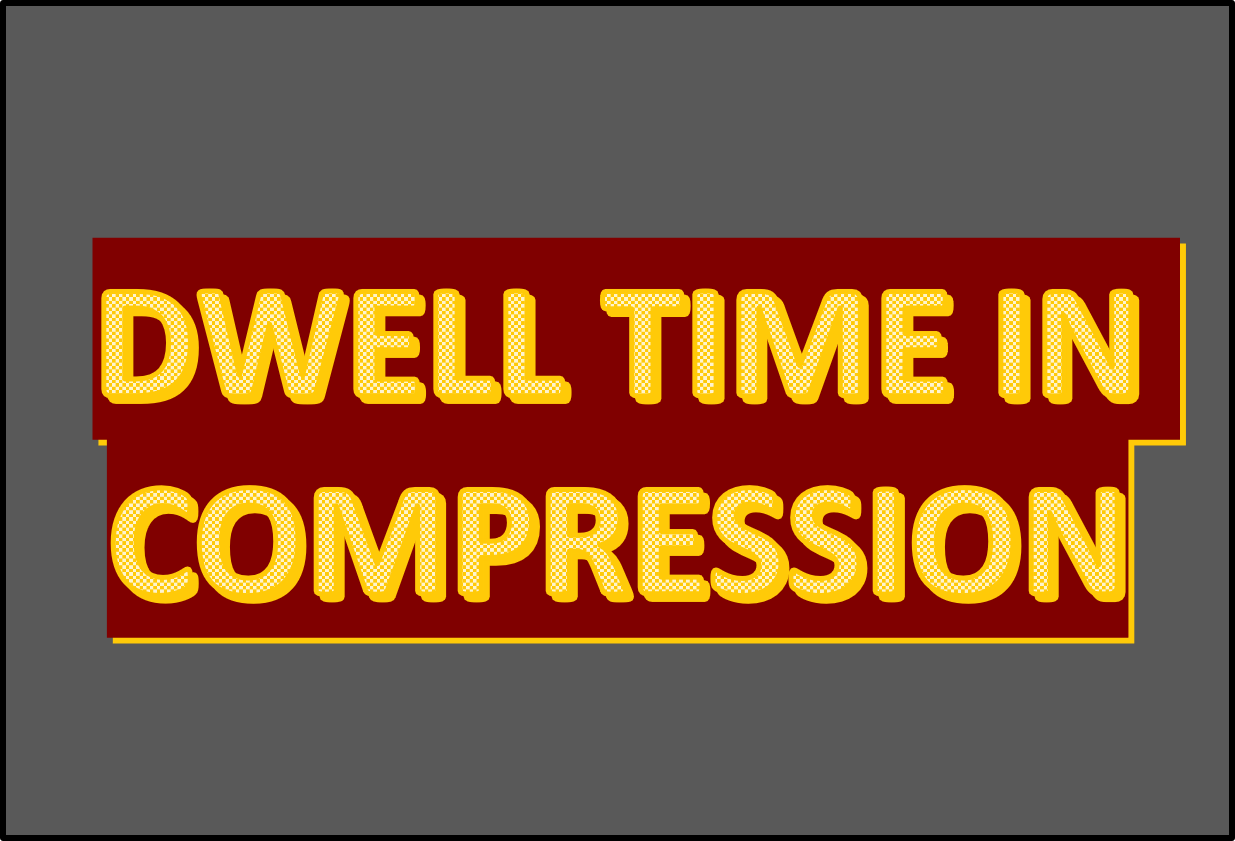
This article provide information about Dwell Time in compression, factors affecting for it and its calculation.
Dwell Time – Art of Tablet Compression
What is mean by Dwell Time In Compression ?
The length of the time the head flat is in contact with the main compression Roller is called Dwell Time. In tableting, it is measured in milliseconds. During this interval the Tablet is undergoing in full compression.
It plays critical role in tablet manufacturing processes. Understanding how it works and can help improve the results of the manufacturing process for many types of tablet products.
Difficult product to compress or issues like capping and lamination may consider increasing dwell time will resolve the same. However, it’s important to note that if you have an air entrapment issue and because of that capping or laminations are generating during compression in that case tapered dies and pre-compression are also great options to reduce those issues.
While in some tableting formulations, dwell time doesn’t need to be considered and are not dwell sensitive. Every formulation will be and will act differently under compression forces as they contain elastic properties so may or may not be require a longer dwell time to force the particles to bond.
Factors Affecting Dwell Time in compression :
Below Main Two Factors are affecting the dwell time in compression i.e. Punch Head Flat size and Speed of the Compression machine.
Punch Head Flat Size : As the compression roller comes into direct contact with head flat so the size of head flat will impact on dwell time i.e. More the head flat size, dwell time will increase or vice versa hence the size is important. Changing from B to D type tooling will extend your head flat and increase your dwell time but can be costly and require modification to your tooling and require new machine.
Compression Machine Speed : The speed of Tablet Compression machine will affect how fast your punches will pass through the compression rollers. One of the most easiest way to generate extra dwell time is to decrease the speed of compression machine, ensuring your punches are being compressed at their peak value for longer. But significant drawback of this is the less output.
How To calculate Dwell Time in compression :
Formula to calculate dwell time in compression is as below
Dwell Time = 6000 x Punch Head Flat in mm / π x Turret Speed x Turret Diameter in mm
Dwell Time = ____________ M/S (Milliseconds).
One example of Dwell Time in compression with Calculation :
Case I : for 51 station – D Type Tooling Machine with the speed of 12 RPM for Compression machine
Head Flat = 18.00 mm (This value can be taken from Punch Drawing)
Turret Diameter : 820 mm (This value will get in Equipment Manual)
π : 3.14
Turret Speed/Turret RPM : 12 (This value will get on machine HMI)
Dwell Time : 6000 x 18 / 3.14 X 12 x 820
Dwell Time : 3.495 m/s
Interference : : On 51 station D Tooling Machine if your RPM is 12 the Dwell time will be 3.495
Case II : Will increase the speed of compression machine by 24 RPM (Double than case I) and rest of the parameter will be same as like Case I
Dwell Time : 6000 x 18 / 3.14 X 24 x 820
Dwell Time : 1.748 m/s
Interference : On 51 station D Tooling Machine if your RPM is 12 the Dwell time will be 1.748 m/s so
Conclusion : By seeing the both results of it can be conclude that, if speed of the compression machine increases the dwell time will decrease. in other words Increase in the speed of the compression machine, punch head flat contact time decreases with main compression Roller.
Image I : B and D tooling Head Flat Difference Image II : B Tooling Punch with standard head Flat , Extended Head flat and Dome shaped
Note : While Designing of Tooling Head Flat can be Increased or Decreased as per product Requirement.