Granulation Process In Tablet Manufacturing- A Comprehensive Approach
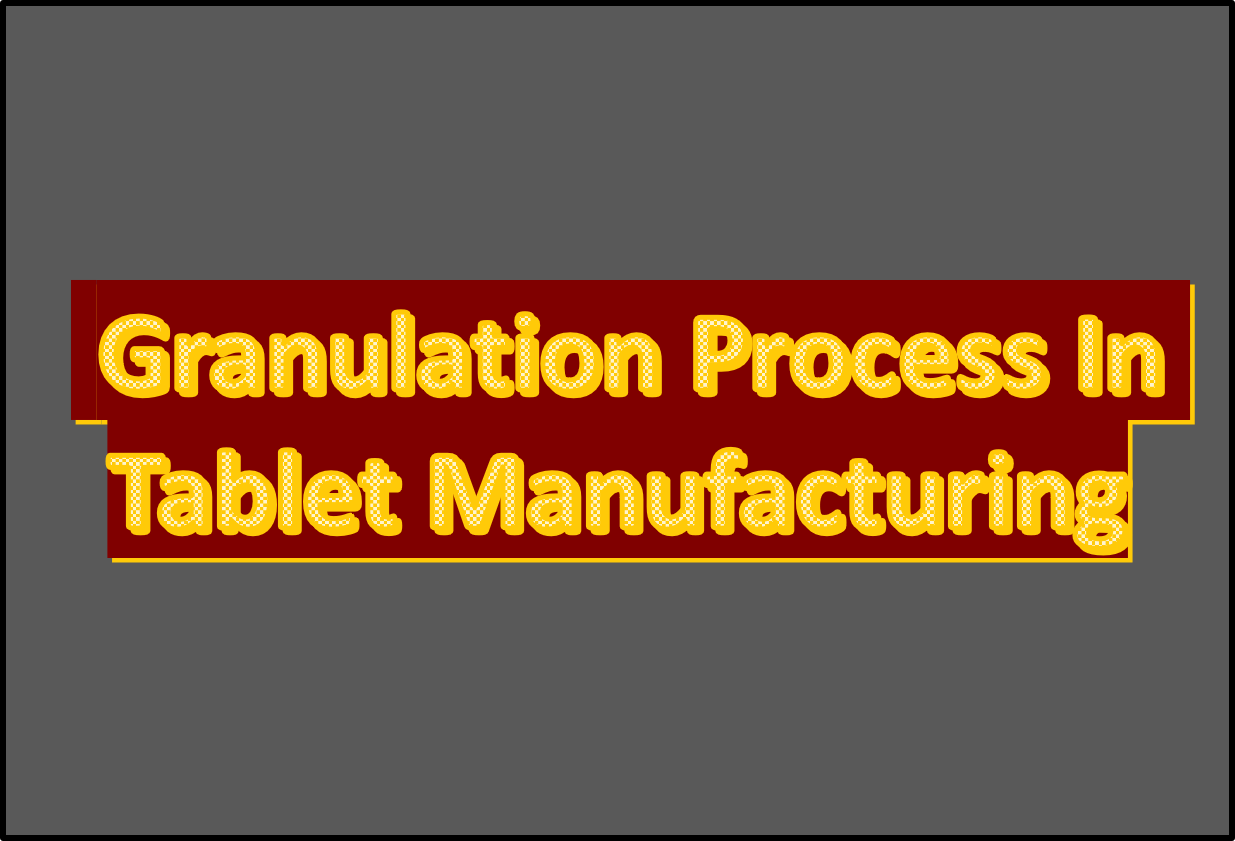
It describes the Granulation process in Tablet Manufacturing i.e. Wet/Dry Granulation, Milling, Blending/Lubrications.
What is mean by Granulation Process in Tablet manufacturing?
Granulation is the process in which powder particles are made to adhere by addition of binder or by compaction to form agglomerates called granules.
Granulation in pharmaceuticals refers to the process of forming granules or small particles from powders or other substances. This process is commonly used in the production of tablets, capsules, and other dosage forms.
During granulation process in tablet manufacturing, the powder is mixed with a liquid binder to form small agglomerates or granules. The granules are then dried, screened, Blending and Lubrications to achieve a consistent particle size and shape. or Powders are slugged/Compacting forms the slugs/Compacts and furthermore this slugs and Compacts will undergo screening, blending and Lubrication process to form a Lubricated Granules ready for Tablet Compression or Filling in EHG shell.
Why Granulation is Required ?
- To Improve the flow properties of mix/Granules.
- To Reduce Dust formation during compression of Mix/Granules
- To change the particle size distribution, so that bulk density can be improved for compressibility.
- To prevent segregation of the constituents of the mix.
- Granules being denser than powder, hence more convenient for storage/shipment and further processing.
- Granulation can improve or modify drug release profile.
Types of Granulation ?
Dry Granulation :
In Dry Granulation Techniques, particle adhesion takes place because of applied pressure. A powder compact or powder sheet is produced which is larger than the granule size required, and therefore the required size can attained by milling and sieving. it is also called the Direct compression Technique.
In elaborative way it can be explained as, This technique involves the compaction of powders without the use of any liquid binder. The powders are first mixed and then compressed into slugs/sheets using a roller compactor. The slugs are then broken down into granules of the desired size using a mill. Dry granulation process in tablet manufacturing is suitable for drugs that are sensitive to moisture or heat, as it does not involve any liquid. However, it may result in poor compressibility and flow properties.
Dry Granulation :
The Dry granulation process is used to form granules without using a liquid solution because the product to be granulated may be sensitive to moisture and heat. Forming granules without moisture requires compacting and densifying the powders. Dry granulation can be conducted on a tablet press using slugging tooling or on a roller compactor commonly referred to as a When a tablet press is used for dry granulation, the powders may not possess enough natural flow to feed the product uniformly into the die cavity.
The dry granulation process in tablet manufacturing is used to form granules without using a liquid solution because the product to be granulated may be sensitive to moisture and heat. Forming granules without moisture requires compacting and densifying the powders.
Slugging Operations :
Sluggers :
The dry powders can be compressed using a conventional tablet machine or, more usually, a large heavy-duty rotary press can be used. This process is often known as ‘slugging’, the compact made in the process (typically 25 mm diameter by about 10–15 mm thick) being termed a ‘slug’. A hammer mill is suitable for breaking the compacts.
Roller Compactors :
Roller Compaction is an alternative Dry Granulation Method, In this method powder mix is being squeezed between two rollers and form a compressed sheet . The sheet normally is weak and brittle and breaks immediately into flakes. These flakes need gentler treatment like Milling operations to break them into granules, and this can be usually common method to form granules with Dry Granulation Method.
Wet Granulation :
Wet granulation involves the addition of a liquid binder to the powders to form granules. The liquid binder mixed with the powders and distributed throughout the powder by mechanical agitation of the granulator. The particles adhere to each other because of liquid film and by further agitation and more liquid addition causes more particles to adhere. The granules are then dried and sieved to get the desired particle size of granules. The precise mechanism by which a dry powder is transformed into a bed of granules varies on the basis of different types of materials used and parameters set during the process.
Wet granulation process in tablet manufacturing is the most commonly used technique in the pharmaceutical industry as it produces granules with good compressibility and flow properties.
Types of Wet Granulation :
Further Wet Granulation generally classified on the basis of Manufacturing Process :
- By using Planetary Mixer
- By using Rapid mixer granulator (RMG)/ High speed mixer Granulator (HSMG)
- By using single pot processor i.e. Fluid Bed Equipment (FBE)
Will see each Technique In Details :
By using Planetary Mixer :
- Planetary mixer is used for wet mixing of the powders, Powder mixing usually has to be performed as a separate operation using suitable mixing equipment.
- The mixed powders are fed into the bowl of the planetary mixer and start the mixer
- Start the mixer and granulating liquid i.e Binder is added slowly and continuously on the powder.
- Paddle of the mixer is responsible for wet mixing and kneading action required to form the granules.
- The paddle of planetary mixer has planetary motion. Design of mixer is such that there is a bare minimum clearance between wall of mixer and blades.
Safety precautions during operation and change over
- Machine earthing must be checked.
- After loading the material, the blade must be properly fixed and the bowl must be locked.
- During loading and unloading and fixing of agitator blade, the electrical mains must be put off.
- Before loading the product blank run should be taken to check for abnormality if any.
- Functioning of emergency switch to stop the mixer must be checked before starting the operations.
By using Rapid mixer granulator (RMG) / High Speed Mixer Granulator (HSMG) :
- The mixer contains a Bowl mounted in vertical position.
- A high speed mixer blade called as agitator revolves around the bottom of the bowl and is responsible for wet mixing and Kneading action of of the granules
- The mixer also contains a high speed chopper blade which functions as lump or agglomerate breaker.4.The Agitator is specially constructed to discharge the material from getting under it.
Safety precautions to be taken during operation and machine changeover.
- Compressed air should be start before initiating the operation.
- Before scrapping the material ensure that the agitator blade and chopper are not in motion.
- During changeover the electrical panel board, PLC and electrical motor for chopper, motor for lifting and positioning device must be covered with polybag.
- During washing and scrapping of the equipment main switch must be off.
- Operator should not insert hand in discharge port during unloading of wet granules.
- Nuts and bolts must be checked before starting the operation.
- During manual checking of end point during granulation ensure that motion of agitator and chopper are stopped completely.
- Never bypass any safety interlock to operate the machine.
- Never touch the moving parts of machine.
- Do not touch the RMG lid without locking rod.
- Check for any unwanted material inside the bowl.
By using single pot processor i.e. Fluid Bed Equipment (FBE) :
- Fluidized bed equipment granulation is a process that involves the spraying of a liquid binder onto a bed of powder in a fluidized state results formation of agglomerates or granules and in continuation it should be dried. Then dried granules are Sieved through different required sieves to obtain required size Granulation. The preferably FBE granulation process should be performed in continuous mode.
2. During changeover main switch must be kept off. Solid flow monitor system must be on during the operation. Main switch (emergency switch) must be put ‘off’ at the end of operation or end of day which ever is earlier.
3. Inflatable gasket must be handled carefully to avoid any rupture during cleaning and positioning of the same in proper place.
4. Ensure that while cleaning & maintenance filter assembly, operator must wear proper headgear and remain clear of area under filter assembly.
5. Check and ensure earthing between processors main body and FBE bowl which is in interlocked. In QASV (Quick Action Stop Valve) Nitrogen gas cylinder is provided with pressure gauge (Range 0 –160 bar). Ensure that the pressure should always be 75 bar (filled condition)Before starting the processor, wait for 1 minute to dissipate the static charge. After stopping the processor, shake the bag for removing the material. Wait for 2 minutes before detaching the bowl.
Binders Used in Wet Granulations :
Generally water is used for wet Granulations and that may adversely affect drug stability, causing hydrolysis of susceptible products and it needs a longer drying time than organic solvents. This increases the length of the process and again may affect stability because of the extended exposure to heat.
Occasionally non aqueous solvents or solutions that are composed of water or water miscible solvents are used to improve the granulation properties of formulation.
Whenever non aqueous solvents are used in granulation reduced amount of energy is required for drying. This gives requirement of proper ventilation and safety precautions against Fire, toxicity and explosion
Safety precautions to be taken during operation and machine changeover of Fluid Bed Equipment :
- Whenever non aqueous solvents are used proper ventilation should be given to granulation area.
- Fluidized bed granulator Proper safety precautions should be taken against fire, explosion and toxicity.
- In fluidized bed granulator dust explosion can take place with flammable solvents. Proper precautions should be taken.
- Static charge can develop inside the FBD of fluidized bed granulator therefore the equipment must be provided with explosion relief panel.
Milling Operations :
The objective of granules milling is to achieve uniform particle size distribution, increase the surface area of the particles for better dissolution, and improve flow properties of the material. This method is processed after drying of wet Granules and Slugged Compacts after Roll Compacting.
Granules Milling can be performed using various types of equipment like Cone Mill, Multimill and Ball mill. widely in pharmaceutical Industry Cone mill being used to perform Milling Operations.
The milling process also helps to remove any oversized or undersized particles, resulting in a more consistent final product.
Blending and Lubrication Operations :
Blending is the process of combining different powdered materials to create a homogeneous mixture. This process is essential in the pharmaceutical industry as it ensures that the active ingredients are evenly distributed throughout the final product. Blending can be carried out using various equipment, including V-Blenders, Bin Blenders and Octagonal Blenders.
Lubrication is the process of adding a small amount of lubricant to the blended powder mixture to improve its flow properties. This process is necessary to prevent the powders from sticking to the equipment during processing and to reduce the friction between the particles. Lubricants used in the pharmaceutical industry are generally food-grade and include materials such as magnesium stearate and stearic acid.
The blending and lubrication processes are often carried out together and are typically performed after granulation and milling. The process may also involve sieving the mixture to remove any oversized or undersized particles and to ensure that the final product has a consistent particle size distribution.